- Bargain Basement
- Abrasive Blasting
- Adhesion
- Ambient Conditions
- Cases
- Cathodic Protection
- Coating Test Panels
- Coating Thickness Gauge
- Combination Gauges
- Compliance Programs
- Concrete Testing
- Corrosion Coupon Test Kits
- Dry Film Thickness Gauges
- Field Microscopes
- Gloss & Appearance
- Hardness Testing
- Holiday/Pinhole Detection
- Inspection Instrument Kits
- Miscellaneous
- Moisture Detection
- Powder Coating
- Publications
- Surface Cleanliness
- Surface Contamination Test Kits
- Surface Profile
- Wall Thickness Gauges
- Wet Film Thickness Gauges
Custom Steel Test Panels
Facility owners and coating manufacturers often evaluate the performance of newer formulations and candidate coating systems on a smaller scale prior to large scale installation on the actual structure. This is particularly important when newer technology coating systems are being considered for use, or when formulation changes are necessary to conform to strict environmental regulations. To facilitate these evaluations, candidate coating systems may be applied to the actual structure as test patches; however, this process can be time consuming and costly. Alternatively, the candidate coating systems can be applied to test panels that are either mounted on test racks in the field adjacent to the actual structure, mounted on test racks that are placed in industrial or marine environments, or installed into accelerated weathering or corrosion chambers in the laboratory. In this manner, the performance of the coating systems can be compared relative to one another after several months or years in the field, or after several months in accelerated weathering.
KTA Steel Test Panels:
- Are fabricated from hot rolled carbon steel, which is the primary type of steel used on industrial structures (hot rolled steel and cold rolled steel have different corrosion rates)
- Conform to ASTM D7055, Standard Practice for Preparation (by Abrasive Blast Cleaning) of Hot-Rolled Carbon Steel Panels for Testing of Coatings
- Conform to SSPC-PA 15, Material and Preparation Requirements for Steel Test Panels Used to Evaluate the Performance of Industrial Coatings
- Can be prepared to various levels of surface cleanliness (e.g., SSPC-SP6, SSPC-SP10, SSPC-SP5)
- Can be prepared with different surface profile depths, from 1 mil (25 µm) up to 5 mils (125 µm) without distortion/warping
- Can be prepared with various abrasive types (e.g., steel grit, steel shot, garnet, aluminum oxide, copper slag, coal slag, nickel slag, etc.)
- Can be purchased in quantities as small as 30
- Are prepared to order, so various sizes are available with or without a hanging hole. No custom upcharges!
Request Custom Steel Test Panels
All fields are required
Steel Test Panel Options
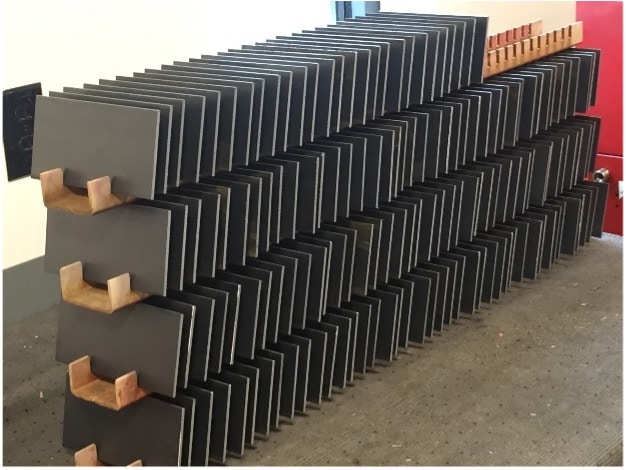
Flat Steel Test Panels
KTA Steel Flat Panels are available in a variety of widths and can be custom cut to nearly any length. Standard thicknesses include 1/16”, 1/8”, 3/16” and ¼”. Common sizes include 3” x 6”, 4” x 6”, 4” x 8” and 6” x 12”. Flat steel test panels are fabricated from hot-rolled carbon steel, and a hanging hole and stenciled letter/number code is available at an additional charge.
KTA Steel Panels can be shipped as fabricated (mill scale bearing hot rolled steel), or can be abrasive blast cleaned, wrapped in corrosion inhibitive (VPI) paper, sealed in plastic (packs of 10/each), and shipped ready to coat. Standard abrasive blast cleaning is performed on both panel faces and edges using steel grit to produce an angular 2-3 mil surface profile and SSPC-SP 10/NACE No. 2, “Near-White Metal” cleanliness. Other surface profile depths and/or levels of cleanliness are available at an additional charge.
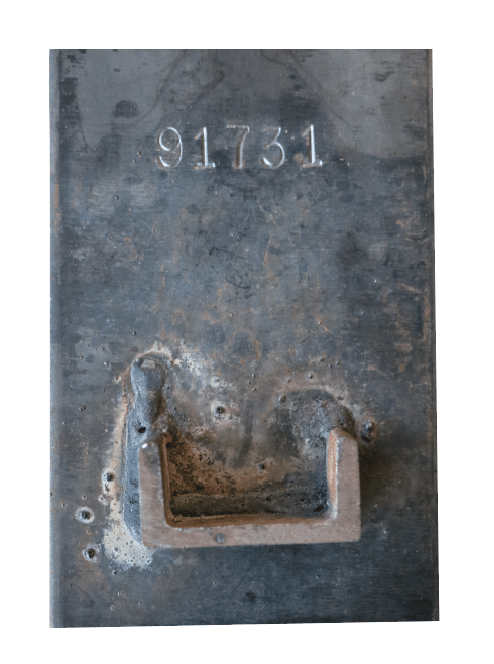
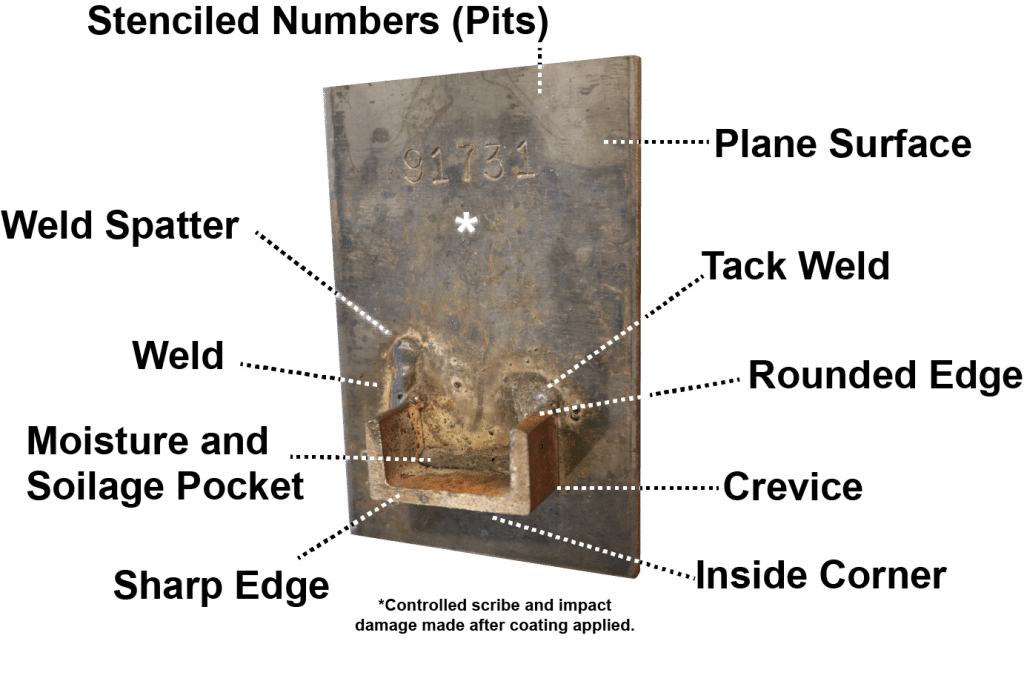
KTA Steel Composite Test Panels
Facility owners and coating manufacturers often evaluate the performance of newer formulations and candidate coating systems on a smaller scale prior to large scale installation on the actual structure. This is particularly important when newer technology coating systems are being considered for use, or when formulation changes are necessary to conform to strict environmental regulations. To facilitate these evaluations, candidate coating systems may be applied to the actual structure as test patches; however, this process can be time consuming and costly. Alternatively, the candidate coating systems can be applied to test panels that are either mounted on test racks in the field adjacent to the actual structure, mounted on test racks that are placed in industrial or marine environments, or installed into accelerated weathering or corrosion chambers in the laboratory. In this manner, the performance of the coating systems can be compared relative to one another after several months or years in the field, or after several months in accelerated weathering.
Flat test panels are frequently used because they are easier to coat. However, most industrial and marine structures aren’t flat. They are frequently complex structures with welds, crevices, collection pockets, edges and a variety of other configurations that are difficult to coat and protect. Coating systems that may perform well on flat surfaces may or may not perform the same on designs that are more conducive to corrosion.
The KTA Steel Composite Test Panel was designed to simulate as much as feasible the irregular surfaces that are often found on complex industrial and marine structures, and that pose a significant challenge for many coating systems. Invented in the 1940’s by the late Kenneth Tator, this test panel design incorporates over ten different evaluation points on a single 4-inch by 6-inch panel. Each panel consists of a 3/16-inch by 4-inch by 6-inch flat ASTM A36 hot-rolled carbon steel plate with a 1-inch deep by 2-inch wide carbon steel channel welded to the face.
The evaluation points that are included in the panel design include: plane surfaces; projections at corners and protrusions created by weld spatter intentionally left on surfaces adjacent to welds; rough welds; crevices; inside corners; moisture and soilage pockets; sharp edges and broken edges prepared using a grinder; pitted surfaces created using a series of stenciled numbers that are also used to uniquely identify the panels; and mechanical damage created by an intentional direct impact and/or an intentional scribe through the coating system to expose the underlying steel. These latter two grading areas are used evaluate a coating’s resistance to rapid impact damage and corrosion undercutting, since mechanical damage in the field is inevitable.
According to Mars Fontana in his book Corrosion Engineering, experience has shown that results obtained on the KTA Steel Composite Test Panel correlate closely with results from coatings on actual equipment, and that coatings that cannot protect well are typically revealed after relatively short exposure periods.
KTA Steel Composite Panels can be shipped as fabricated (mill scale bearing hot rolled steel), or can be abrasive blast cleaned, wrapped in corrosion inhibitive (VPI) paper, sealed in plastic (packs of 10/each), and shipped ready to coat. Standard abrasive blast cleaning is performed on all surfaces using steel grit to produce an angular 2-3 mil surface profile and SSPC-SP 10/NACE No. 2, “Near-White Metal” cleanliness. Other surface profile depths and/or levels of cleanliness are available at an additional charge.
The evaluation points that are included in the panel design include: plane surfaces; projections at corners and protrusions created by weld spatter intentionally left on surfaces adjacent to welds; rough welds; crevices; inside corners; moisture and soilage pockets; sharp edges and broken edges prepared using a grinder; pitted surfaces created using a series of stenciled numbers that are also used to uniquely identify the panels; and mechanical damage created by an intentional direct impact and/or an intentional scribe through the coating system to expose the underlying steel. These latter two grading areas are used evaluate a coating’s resistance to rapid impact damage and corrosion undercutting, since mechanical damage in the field is inevitable.
Why Purchase Test Panels from KTA?
Whether you are a coating/lining manufacturer, facility owner, or original equipment manufacturer, you likely rely on performance data from prepared and coated test panels to evaluate new paint formulations prior to going to market or evaluate candidate coating systems on a smaller scale prior to large scale installation on the actual structure or component. The substrate and the surface preparation prior to coating must be done correctly and consistently to isolate the performance of the coating/lining without bias from the underlying surface. While the metallurgy of the steel itself can be hard to control, the surface preparation of the steel is not. KTA understands the importance of surface preparation and both the direct and indirect (automatic) requirements of the SSPC Surface Preparation Standards. We:
- Solvent clean prior to abrasive blast cleaning (per SSPC-SP 1)
- Monitor the compressed air for cleanliness (per ASTM D4285)
- Monitor the abrasive cleanliness (per ASTM D4940 and D7393) for both water-soluble contaminants and oil
- Assess post-blast surface cleanliness using the SSPC-VIS 1 Guide
- Measure surface profile (per ASTM D4417, Method C)
- Remove visible surface dust using clean, dry compressed air (ASTM D4285)
- Handle all prepared panels using gloved hands
KTA’s name is synonymous with quality, and the production of test panels for coating performance evaluation studies is no different from our other products and services. KTA
has a formal procedure (IS-016) that covers the quality processes associated with:
- Solvent cleaning of the fabricated test panels,
- Testing the oil content and water-soluble contaminants of the abrasive media,
- Communicating the specified degree of surface cleanliness and surface profile depth to the blast cleaner,
- Verifying compressed air cleanliness,
- Abrasive blast cleaning of the fabricated test panels,
- Removing abrasive and surface dust from the prepared steel panels,
- Visually assessing and documenting surface cleanliness,
- Measuring and documenting surface profile depth, and
- Packaging for shipment.
A completed Test Panel Preparation Documentation Form (IS-016F) is sent with every order.
Abrasive blast cleaned test panels are of no use if they are not protected from the environment during shipment and begin to corrode before they even arrive. Immediately after blast cleaning and quality checks are performed, the test panels are wrapped in packs of 10 using VPI paper (rust inhibitive) and sealed in plastic. The wrapped and sealed packs are placed into new boxes and the box weight monitored. Large shipments are palletized, banded, protected with plastic and shipped freight to effectively eliminate individual box handling until the shipment arrives.
Our test panel packaging is so good that it is difficult to determine what is on the inside of the packaging without opening them. So we place a custom, self-adhesive label on the outside of every pack and box that includes the Purchase Order No., date, substrate type, panel size, cleanliness level, and surface profile range.