- Bargain Basement
- Abrasive Blasting
- Adhesion
- Ambient Conditions
- Cases
- Cathodic Protection
- Coating Test Panels
- Coating Thickness Gauge
- Combination Gauges
- Compliance Programs
- Concrete Testing
- Corrosion Coupon Test Kits
- Dry Film Thickness Gauges
- Field Microscopes
- Gloss & Appearance
- Hardness Testing
- Holiday/Pinhole Detection
- Inspection Instrument Kits
- Miscellaneous
- Moisture Detection
- Powder Coating
- Publications
- Surface Cleanliness
- Surface Contamination Test Kits
- Surface Profile
- Wall Thickness Gauges
- Wet Film Thickness Gauges
Calibration, Verification of Accuracy and Adjustment… Synonyms or Differences in Terminology?
“Do I have to maintain inspection gage calibration and certification? Why don’t they retain their calibration over time? Do I need to verify gage accuracy on a regular basis? How often? What is the difference between calibration and verification of accuracy?”
These are common questions in the coatings industry. A simple answer is that without routinely calibrating/certifying coating inspection gages using standards traceable to a national metrology institution and verifying the accuracy of your equipment prior to use, the gages only reveal values, and there is no way to determine whether those values are representative. Quality Assurance and Quality Control inspectors have an obligation to make certain that the values being displayed by the gages are accurate and represent the quality of the work performed, as decisions regarding acceptability of work performed, or the need for rework are made based on gage readings. So, calibration and verification of accuracy are both important, but are distinctly different.
Differentiating Calibration from Verification of Accuracy and Adjustment
Calibration is defined as a controlled and documented process, and is performed by the gage manufacturer, their authorized agent, or by an accredited calibration laboratory. Calibration must be performed in a controlled environment that is not typically found in a shop or in the field.
Verification of accuracy is performed by the gage operator and does not need to be performed in a controlled environment. Based on the accuracy verification process, adjustments may be necessary to compensate for shop or field conditions during the measurement process. An example, based on a dry film thickness gage is provided below.
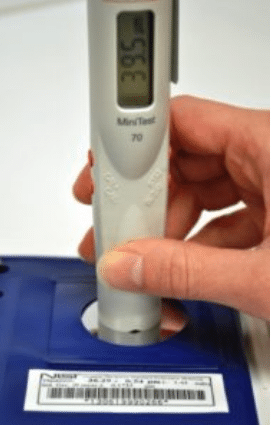
ASTM D7091, Standard Practice for Nondestructive Measurement of Dry Film Thickness of Nonmagnetic Coatings Applied to Ferrous Metals and Nonmagnetic, Nonconductive Coatings Applied to Non-Ferrous Metals and SSPC-PA 2, Procedure for Determining Conformance to Dry Coating Thickness Requirements both contain information on calibration, verification of accuracy and adjustment (incidentally, all three are required prior to obtaining coating thickness measurements when one or both of these standards are invoked by the project specification). For electronic gages (known as Type 2 gages), verification of accuracy is performed using traceable, certified coated standards or using certified shims placed on smooth metallic substrate. This is typically accomplished by using coated standards or certified shims that are slightly below and slightly above the anticipated dry film thickness range (known as two-point verification).
SSPC-PA 2 states that verification of accuracy should be performed (at a minimum) at the beginning and end of each work shift, and recommends verifying accuracy during measurement acquisition, especially if a large data set is being obtained or the gage is dropped or suspected of being out of tolerance. This step makes certain that the gage is working properly, but another step, adjustment, is necessary before using the gage to measure coating thickness.
Adjustment is the act of aligning a gage to correct for substrate metallurgy, curvature, roughness (including surface profile), and other characteristics that may affect the measurements. This is accomplished by placing certified or measured shims onto the prepared, uncoated substrate and adjusting the gage to align with the shim value. One point or two point adjustments using shims may be performed. After this step, the instrument is ready for use in measuring coating thickness.
Alternatively, after verification of accuracy is performed a series of 10 or more Base Metal Readings (BMRs) can be obtained from the prepared, uncoated surface. The average BMR is deducted from the coating thickness. BMR is not the same as surface profile. Surface profile is defined as a measurement of the maximum, peak-to-valley depth created by abrasive blast cleaning and some rotary impact power tools. BMR is the effect of this roughness on a coating thickness gage. For example, a 3-mil surface profile may yield an average 0.7 mil BMR. Never deduct surface profile from coating thickness measurements.
By adjusting the gage to a known thickness over the prepared surface (i.e., using a measured shim) or by measuring and deducting a BMR, the thickness of the coating above the peaks of the surface profile is revealed.
While the focus of this column has been on dry film thickness gages, any gage that takes a measurement should be calibrated (typically annually). This includes temperature gages, micrometers, pressure gages, conductivity and pH meters and any other instrumentation used to verify the quality of workmanship.
Matt Fajt is a Vice President and Business Unit Manager for the Instrument Sales and Service Group for KTA-Tator, Inc. He is an NACE Level 2 certified coatings inspector, SSPC PCI Level 1 and a frequent workshop facilitator on inspection instrument use. He can be reached at mfajt@kta.com.