- Bargain Basement
- Abrasive Blasting
- Adhesion
- Ambient Conditions
- Cases
- Cathodic Protection
- Coating Test Panels
- Coating Thickness Gauge
- Combination Gauges
- Compliance Programs
- Concrete Testing
- Corrosion Coupon Test Kits
- Dry Film Thickness Gauges
- Field Microscopes
- Gloss & Appearance
- Hardness Testing
- Holiday/Pinhole Detection
- Inspection Instrument Kits
- Miscellaneous
- Moisture Detection
- Powder Coating
- Publications
- Surface Cleanliness
- Surface Contamination Test Kits
- Surface Profile
- Wall Thickness Gauges
- Wet Film Thickness Gauges
What is a Base Metal Reading and How Does It Effect Coating Thickness Measurements?
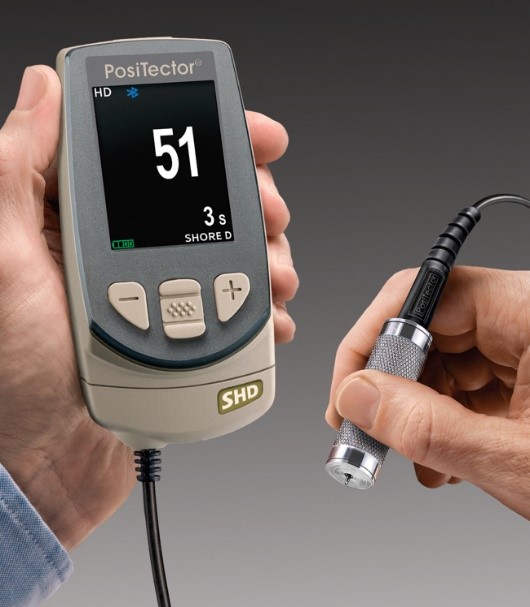
For many in the health care/fitness industry, BMR is an acronym for basal metabolic rate. Sorry to disappoint if you thought this would be a health science article about expending energy. Rather, this article is about a different BMR: Base Metal Reading. We’ll describe what it is, its significance, how to obtain it, and how it impacts coating thickness.
Introduction to Coating Thickness Standards
There are two common industry standards that govern measurement of coating dry film thickness on metal substrates, including ASTM D7091, Standard Practice for Nondestructive Measurement of Dry Film Thickness of Nonmagnetic Coatings Applied to Ferrous Metals and Nonmagnetic, Nonconductive Coatings Applied to Non-Ferrous Metals and SSPC-PA 2, Procedure for Determining Conformance to Dry Coating Thickness Requirements. Both address the use of Type 1 (magnetic pull-off) and Type 2 (electronic) gages as well BMR acquisition. SSPC-PA 2 also addresses measurement frequency and the acceptability of the measurements.
What is BMR?
BMR is the effect of substrate roughness on a coating thickness gage. The roughness is created by preparation of the substrate (e.g., abrasive blast cleaning or power tool cleaning), which generates a surface texture or “profile,” or by a manufacturing process that imparts roughness into the substrate. Instruments that measure the dry film thickness of the applied coating reach part way down into the roughened metal surface to operate properly (illustrated by the red line). However, specifications list the required coating thickness as measured from the tops of the peaks of the surface profile (illustrated by the blue bar). This inherent delta is known as the base metal effect. It is deducted from the coating thickness measurements to eliminate any effect of surface roughness. If the BMR is ignored, the thickness of the coating from the tops of the peaks of the surface profile may be overstated.
Acquisition of a BMR is not predicated on the gage type (Type 1 magnetic pull-off verses Type 2 electronic), but rather the way the gage is set-up by the operator to compensate for surface roughness. For both Type 1 (see photo, left) and Type 2 gages a BMR may be acquired and deducted from the coating thickness.
As an alternative, for Type 2 gages one or more measured shims (one shim is considered a one-point adjustment while the use of two shims spanning the range of intended use is considered a two-point adjustment) may be placed onto the prepared (roughened) metal surface and the gage adjusted to correspond to the shim thickness, effectively removing any need to measure and deduct a BMR. According to SSPC-PA 2, these measured shims are not permitted to be used with Type 1 gages unless explicitly allowed by the gage manufacturer, so in most cases a BMR will be required when using a Type 1 gage.
Obtaining Base Metal Readings
Section 6.2 in SSPC-PA 2 states, “To compensate for any effect of the substrate itself and surface roughness, obtain measurements from the bare, prepared substrate at a minimum of ten locations (arbitrarily spaced) and calculate the average value. This average value is the base metal reading.” Here are the steps:
- Verify the accuracy of the coating thickness gage before use. Traceable coated standards are required for both Type 1 and Type 2 coating thickness gages.
- Obtain a minimum of ten readings on the prepared, uncoated substrate in random locations. To avoid forgetting to acquire a BMR, it is best to take the measurements at the same time surface profile measurements are obtained.
- Measure the coating thickness.
- Deduct the average BMR.
The BMR is not only deducted from the primer thickness, but the cumulative layer thickness measurements as they are obtained. This is illustrated below:
Measured primer thickness: ———————————————————- 4.9 mils
BMR: ———————————————————————————— (0.6 mil)
Actual primer thickness from the top of the peaks of the surface profile: —— 4.3 mils
Cumulative primer & topcoat thickness: ——————————————— 9.2 mils
BMR: ————————————————————————————- (0.6 mil)
Actual cumulative thickness from the top of the peaks of the surface profile: — 8.6 mils
It is important to recognize that BMR and surface profile are related, but they are not the same. Surface profile is a measurement of the maximum peak-to-valley depth created by abrasive blast cleaning or some type of impact power tool. It is measured using one of three methods described in ASTM D4417, Standard Test Methods for Field Measurement of Surface Profile of Blast Cleaned Steel and SSPC-PA 17, Procedure for Determining Conformance to Steel Profile/Surface Roughness/Peak Count Requirements. BMR is the effect of this surface profile on a coating thickness gage. A 3-mil surface profile may have an associated BMR of 0.7 mil. Deducting surface profile from the coating thickness instead of the BMR will result in a significant under-recognition of the actual coating thickness.