- Bargain Basement
- Abrasive Blasting
- Adhesion
- Ambient Conditions
- Cases
- Cathodic Protection
- Coating Test Panels
- Coating Thickness Gauge
- Combination Gauges
- Compliance Programs
- Concrete Testing
- Corrosion Coupon Test Kits
- Dry Film Thickness Gauges
- Field Microscopes
- Gloss & Appearance
- Hardness Testing
- Holiday/Pinhole Detection
- Inspection Instrument Kits
- Miscellaneous
- Moisture Detection
- Powder Coating
- Publications
- Surface Cleanliness
- Surface Contamination Test Kits
- Surface Profile
- Wall Thickness Gauges
- Wet Film Thickness Gauges
What a Good Coatings Inspector Needs to Know
Written by William D. Corbett, COO
AMPP Senior Certified Coating Inspector & Certified Protective Coating Specialist
Introduction
The role of a Coatings Inspector has evolved, and the responsibilities have increased over what used to be a rather straightforward job: to verify that surface preparation and coating application performed by a contractor (or an in-house painting crew) conform to the minimum requirements of the project specification. Decades ago, equipped with the specification and some training on instrument use we set out to watch the contractor sandblast the surface, then mix, thin, and apply the paint (under acceptable conditions) to the correct thickness, then measure the thickness using a magnetic pull-off gage, and be done.
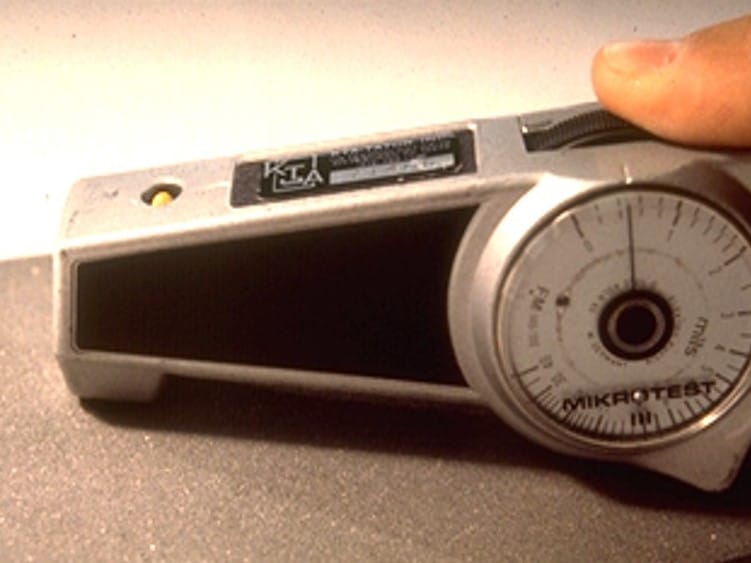
Today there are week-long or multi-week basic and advanced coating inspection training and certification courses; specialty courses that are industry-specific such as bridge, marine, and nuclear power; courses and certifications that are substrate-specific such as concrete coatings inspection; and even coating-specific inspection courses such as inspection of thermal spray coatings. In addition to coatings knowledge gained through course offerings available through associations and private industry, coatings inspectors may also need to be proficient in maintenance and protection of traffic, or worker exposure controls, monitoring of emissions, and waste management processes on hazardous paint removal projects. The value that a well-trained, competent coating inspector (with well-rounded knowledge of various surface preparation methods, coatings, specialty application methods, and industries) brings to a project cannot be overstated. Inspectors can help prevent or reduce rework that adversely impacts schedule and/or results in cost overruns and can help prevent premature coating failure.
Trained and certified coatings inspectors with competency in a variety of coatings, processes, and industries are often expected by the facility owners that hire the individual or the inspection firm. To fulfill this expectation, continuing education has become paramount to stay abreast of new standards and changes to existing ones, new instrumentation, and new coatings technology.
Do we now need a PhD in Coatings Inspection? Not exactly, but this white paper explores the role of a coating inspector as well as the basic skills of a competent coating inspector and the advanced skills that may be expected by facility owners. The goal is to present the roles, responsibilities, knowledge, skills, and attributes of a good coating inspector so that knowledge/experience gaps can be identified, and methods developed (through education, mentoring, and/or experience) to minimize or eliminate those gaps.
The Role and Requirements of a Coating Inspector
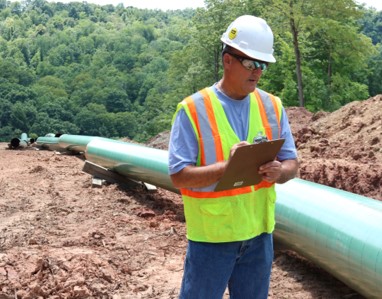
The role of a coating inspector is to Observe, Assess, Document and Report (OADR). That is, Observe the work that has been completed at the hold point, Assess whether the work completed meets the minimum requirements of the project specification, Document the results of the inspection, and Report (communicate) the outcomes to the facility/asset owner (for the role of QA inspector) or contractor management (for the role of QC inspector).
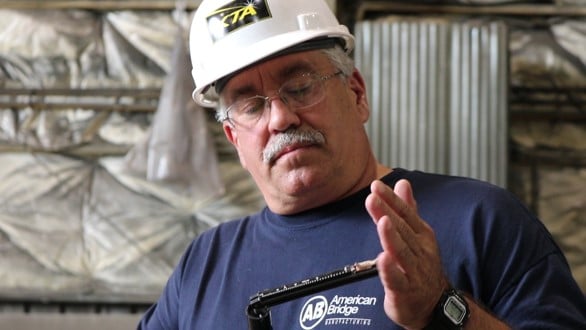
Further distinction is required however, in terms of defining the roles of a quality control (QC) inspector versus a quality assurance (QA) inspector. An article posted on KTA University titled,Roles & Responsibilities of Quality Assurance & Quality Control Personnel on a Coatings Project explores the differences. A QC inspector represents the painting contractor and is responsible for the frequent, routine, systematic inspections to verify each phase of the work meets the requirements set forth by the project specification. Since the painting contractor is ultimately responsible for providing quality workmanship and conforming to the specification, they are in fact controlling quality. Conversely, QA inspectors represent the facility/asset owner and may be part of the owner’s staff or be provided by a 3rd party. QA inspectors verify that quality is being controlled and that QC is being performed correctly and conducted at the frequency required by the specification. In many cases, QA inspectors provide the same level inspection as the QC inspector, but the responsibility for quality remains with the contractor and the QC inspector. If the QA inspector is an employee of the facility/asset owner then they have stop-work authority, whereas a 3rd party inspector working under contract to the facility/asset owner does not, since there is no contractual relationship between the 3rd party QA inspector and the contractor. Nonetheless, the “OADR” role does not seem all that complicated until one uncovers what all is involved.
In Chapter 2 of the SSPC publication, The Inspection of Coatings and Linings[1] the author describes the professional and personal requirements of coatings inspectors. It states that while the specific requirements will vary depending on the nature and purpose of the project, generally the requirements include physical ability, training, experience, written and verbal communication skills, and certain character traits. Ideally the inspector is prepared to respond to all quality issues that arise on a given project.

Physical Ability: Physical requirements of a coatings inspector often include the ability to climb, enter confined spaces, good vision (corrected as necessary) as well as the ability to distinguish colors, and manual dexterity. Climbing and entering confined spaces (as well as other conditions) will require proper use of personal protective equipment such as respirators, fall protection (harnesses and lanyards), and coveralls, which can be physically demanding, so an inspector should be physically fit and, when applicable, comfortable working from heights. Manual dexterity is required to properly use/manipulate inspection instruments that are becoming smaller and smaller for portability, which makes them more challenging to manipulate, especially while wearing gloves.

Training/Continuing Education: Formal training is a critical requirement for a coating inspector. Fortunately, there is no shortage of courses from trade organizations such as the Association for Materials Protection and Performance (AMPP) and FROSIO, as well as from private companies. These courses are frequently instructed by subject matter experts that have performed coating inspection for years, so they have lived and breathed the information conveyed throughout the course delivery. There are two essential components to inspector training: theory (visual/auditory learning) and hands-on (kinesthetic learning). One without the other is ineffective, which is challenging in today’s on-line/virtual microlearning environments that are expected by younger generations. There are frequently varying levels of training, from basic (introductory) to advanced, and there are now experience requirements before progressing from one level to the next.
However, initial training isn’t enough. Like most any occupation, continuing education is a critical component to a coating inspector’s value. Our world is changing exponentially, and the coatings industry is evolving rapidly. Coating specifications frequently reference industry standards that, once invoked by contract become contractual law. Industry standards change. In fact, most standards-writing organizations will review/revise/update their standards every 5-years or so, and new standards are published intermittently. So, without continuing education, a coating inspector that was trained on a specific inspection standard (e.g., coating thickness measurement) in year 2000 could easily be inspecting coating thickness according to a standard that has been revised/updated four times since they were initially trained.
In a technical paper titled, “Industry Standards: Are You Current?”[2] the author described why and how to remain current, then listed ten common coatings industry standards from SSPC, ASTM, NSBA and others that had been updated in the previous two years. Continuing education, particularly on industry standards, inspection techniques, instrumentation, and safety is a critical responsibility of a coatings inspector and a requirement of the AMPP-SSPC-QP 5 certification program[3]. While AMPP-SSPC-QP 5 certification is applicable to inspection companies and not individual inspectors, it does contain the physical requirements, duties, and the education, certification and experience requirements of coating inspectors that are worth reviewing by any coating inspector, not just those employed by the certified coating and lining inspection company.
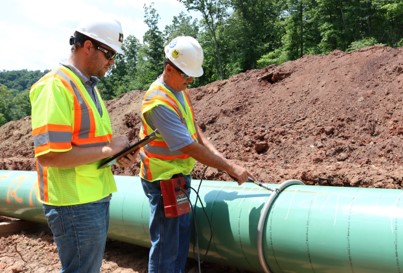
Experience: Training without experience and experience without training can result in under- or over-inspection and poor quality. The point is that an inspector needs both to be of value to a facility/ asset owner. How often have we heard, “… now that you’ve completed your basic training hurry up and get 5 years of experience so we can get you to the next level?” Experience takes time, and there is both good and bad experience. In Chapter 2 of SSPC’s The Inspection of Coatings and Linings the author states that on-the-job training is best obtained by working under the supervision of an experienced inspector, and the supervising inspector should monitor the trainee’s work regularly to ensure that standard test procedures and practices are followed. This statement is accurate (and arguably the way the AMPP Coating Inspector Certification levels are intended), but it assumes the supervising inspector has the skills and attributes of a mentor and coach, and not just the technical knowledge. It also assumes project budgets can support two levels of inspectors. Nonetheless, experience is and should remain a requirement of a competent coating inspector, and a formal mentoring/coaching program (post-training) should be in the forefront of any certification program. But easier to say than to implement.
Verbal and Written Communication Skills: Another essential requirement of a competent coating inspector is the ability to clearly and concisely communicate both verbally and in writing. The information provided by an inspector must be professional and impartial. Patient, calm oral communication can be particularly challenging when issues arise (and tempers flare); however, the coating inspector should never be arrogant, rude, or excitable. Their role is to communicate the facts and if asked, offer comments on proposed options for corrective actions with the facility owner, specifier, and contractor superintendent.
Written communication is an art, and the ability to communicate using the written word should be a requirement of a competent inspector. Some will argue that written communication has become a lost art and that even the most educated individuals cannot convey their thoughts in a clear, concise, coherent manner. Despite that potential reality, written documentation is of critical importance on a coatings project and is a key element in resolving disputes or premature failure. While the coating specification reveals what was supposed to be done, an inspector’s documentation reveals what was done. Daily inspection reports contain data acquired using instruments, but a properly constructed narrative gives context to the data and provides the owner and the contractor management with a picture of how the project is progressing. As the demand for the use of electronic inspection reports increases, the importance of narrative is only heightened.
Responsibilities of a Coating Inspector
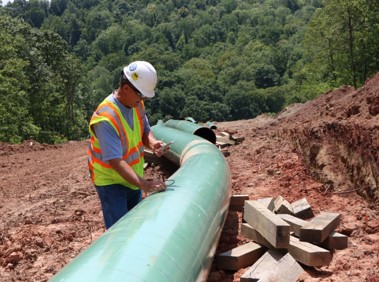
Once the role of a coating inspector is defined and the requirements to achieve and maintain coating inspector status are understood, the specific responsibilities of an inspector can be described. ASTM D3276[4] and ASTM D6237[5] are two common guides. According to their respective scopes, they are designed to aid painting inspectors in carrying out their tasks efficiently. They include the key elements of surface preparation, coatings application, and final approval for both field and shop work.
Common responsibilities of a coating inspector are listed in the Table 1. These responsibilities are generally, but not exclusively, related to inspection of coatings applied to steel; other responsibilities are added when coating concrete or other substrates. As clearly illustrated in the table, the responsibilities are numerous, but not all of them are necessary on a single project. Nonetheless, the competent coating inspector needs to be proficient in all responsibilities of all phases listed in the table. Interestingly, there are nine responsibilities before the project truly begins (“Pre-Project”). The inspection checkpoints denoted with a * are frequently contract specific.
Table 1: Common Coating Inspector Responsibilities by Project Phase
Phase | Responsibility |
Pre-Project | Read & comprehend the project specification; issue requests for clarification. Read and comprehend the coating manufacturer’s product data sheets (PDS); denote conflicts between the PDS and specifications and seek resolution. Read the Safety Data Sheets (SDS) for each hazardous product on the job and know the PPE required. Attend and participate in the Pre-construction Conference. Obtain a copy of the Pre-construction Conference minutes and note changes/clarifications to the project specification as appropriate and be current with all Addendums. Obtain pre-project safety training and/or required medical surveillance. Obtain PPE compatible with jobsite conditions/rules. Verify the type of inspection equipment required for the project; verify operation and accuracy as well as currency of calibration. Prepare an Inspection Plan, as required. |
Materials Receipt/Storage | Verify materials such as cleaners, caulking, abrasive, coatings, thinners, etc. are received and stored correctly. Verify the shelf life of materials has not expired. Record batch numbers of components and thinners. Monitor storage areas for temperature & humidity*. Document all information. |
Pre-Surface Preparation | Verify removal of visible grease/oil, etc. per SSPC-SP 1 Inspect edges, welds, fasteners for coat-ability; verify spatter and lamination removal; inspection of section loss*. Examine the structure for difficult-to-access areas and bring them to the attention of the owner for resolution (if not already addressed by the specification). Conduct surface soluble salt contamination testing (may also be required post-preparation) *. Verify compatibility of surface preparation equipment and expendables (e.g., abrasive) with the specification requirements. Verify protective covering are in place and secure. Verify proper lighting*.Document all information. |
Surface Preparation | Measure ambient conditions and surface temperature prior to final surface preparation. Inspect indirect requirements of SSPC abrasive blast standards. Compressed air cleanliness. Abrasive cleanliness (water-soluble contaminants & oil). Determine initial condition of the steel (Rust grade).Inspect surface cleanliness per level specified. Inspect surface profile depth (and peak density*). Inspect for adequate removal of soluble salts when required after preparation*. Verify adequate dust removal. Verify maximum preparation-to-primer time not exceeded. Document all information. |
Mixing/Thinning | Measure ambient conditions and surface temperature. Verify coating components being mixed are correct. Measure coating material temperature. Verify correct proportions if mixing of partial kits is allowed. Verify proper mixing procedures per PDS. Verify proper type and amount of thinner, if used. Verify induction time per PDS. Verify mix is applied prior to pot life expiration. Document all information. |
Coating Application | Verify compatibility of coating application equipment with the PDS. Measure ambient conditions and surface temperature throughout application at intervals required. Verify stripe coating*. Verify the wet film thickness (WFT) target has been adjusted for thinner amounts added and that applicators are using WFT gages. Verify recoat times (minimum/maximum). Verify intercoat cleanliness and watch for amine exudate formation for certain types of epoxy coatings. Document all information. |
Post-Coating Application | Measure dry film thickness of each coat. Perform pinhole/holiday detection*. Perform hardness/cure testing*. Perform adhesion testing*. Document all information. |
Other (project/role-dependent) | Inspecting duplex coating systems. Verify proper primer application and curing time to faying surfaces of slip-critical connections (per Test —-Certificate/Essential Variables). Verify compliance with OSHA worker lead exposure requirements. Verify containment structure “as built” meets design criteria. Verify ventilation inside containment. Verify protection of air, soil, water, and public adjacent to the worksite, including associated monitoring. Verify waste is segregated, stored, and transported properly. Verify acceptability of site housekeeping. |
Knowledge, Skills, and Attributes
Roles and responsibilities are related to, but different than knowledge, skills, and attributes, or KSAs of a competent coating inspector. For coating inspectors to perform their duties competently they must have the knowledge of industry standards and instrument use, as well as the ability to apply that knowledge to project-specific situations that invariably crop up on nearly every project. The ability to assess a situation, tap into learned knowledge, industry standards, and common sense, and apply that knowledge to help resolve problems as they occur is arguably one of the most valuable and sought-after attributes of a coating inspector. This comes with experience. For a QA inspector it also presents itself as a fine line between helping to resolve issues and directing the work. That too comes with experience.
Knowledge of Industry Standards: As previously described, most coating specifications reference industry standards (e.g., SSPC-SP 10, Near-White Abrasive Blast Cleaning, SSPC-PA 2, Procedure for Determining Conformance to Dry Coating Thickness Requirements, etc.) And many standards reference other standards. Coating inspectors must know the direct and indirect requirements of industry standards as well as the referenced standards within them. For example, for abrasive blast cleaning, they must know how much, if any, staining can remain on the surface (and how it is evaluated), differences between rust back and staining, what qualifies as a dull putty knife as an inspection tool, use of visual aids, how many surface profile readings to acquire in a location and how many locations to measure, requirements for testing the cleanliness of the compressed air, and how to determine specification conformance based on the data acquired. In the case of coating thickness, the measurements themselves are easy. Acquiring coating thickness data at the correct frequency and processing the data to determine acceptability is the difficult part of inspection.
Further, these standards change over time and new standards are developed. It can become a full-time job simply keeping up with industry standards. But knowingly or unknowingly performing inspections that conflict with the referenced standards can be problematic and even potentially lead to litigation. Access to current industry standards is critical for the inspector. It is just as important as the instruments used to perform the inspections.=
Knowledge of Instrument Use: The successful performance of a protective coating system depends on the quality of the surface preparation and coating system installation. To verify quality and specification compliance, inspectors rely heavily on data generated by inspection instruments and on visual inspections of the prepared and coated surfaces. Without proficiency in instrument use and an understanding of how to navigate through SSPC visual guides, it is nearly impossible to determine specification compliance. That is, you can’t tell how thick the paint is unless you measure it. You don’t know if the measurement is right if you don’t know how to use the gage. The publication, Using Coating Inspection Instruments[6], was written to assist inspectors, contractors, facility owners, engineers, coating manufacturers and other coating professionals with the proper use of inspection instruments, guides, and test kits. Many standards reference instrument manufacturer’s instructions for proper use; however, if there are differences between the manufacturer’s instructions and an industry standard, the inspector should obtain clarification prior to project start-up.
Many of the inspection checkpoints listed in Table 1 require the use of instruments, visual guides, or test kits, and new instrumentation routinely comes to the marketplace to fill a void, such as abrasive cleanliness test kits. Proficient use of instruments, guides, and test kits remains a critical function of a competent coating inspector. But instrument use is only part of the equation. A competent inspector must also understand the importance and frequency of calibration (and who is accredited to perform calibration) and the procedures for routine verification of instrument accuracy. Use of uncalibrated inspection instruments is considered by AMPP to be a malpractice ethics violation for a certified inspector.
Character Traits: Imagine if coating inspectors were like fast food chain hamburgers… no matter what, they would all be essentially the same consistency and quality. Knowledge, skills, and attributes of inspectors would be equal, and enforcement of the project specification would be completely uniform. What we are describing is an inspector that is devoid of a personality. As long as coating inspection is performed by humans, we have to consider how personality and character traits play a role. That is, knowledge, skills, and attributes of inspectors will not be equal, and enforcement of the project specification won’t be completely uniform, despite how important these items are to a facility/asset owner and contractor. Personality types and traits is a well-published topic, so the focus herein will be on ethics and judgement.
As the author states in Chapter 2 of The Inspection of Coatings and Linings, a coating inspector must have high personal integrity and a strong work ethic to enforce the specification without personal bias. Frequently an analogy is made between the role of a coating inspector and a police officer: enforce the law without personal bias. Like a police officer, a coating inspector does not write the law (the specification) but is charged with enforcing it without imposing personal standards of quality or workmanship. An inspector must remain constantly aware that the criteria for work acceptance is established by the project specification and not their personal viewpoint as to what will provide the best performance, what the specifier meant, or what will work best. Making concessions to maintain or improve the project schedule is never the role of an inspector. Even the most comprehensive, well-written specification cannot address every possible problem/challenge that may arise on a project, so some knowledge-based judgement on the part of the contractor, inspector, and owner will occasionally be required. However, the role of the inspector is not to interpret or modify the specifications without the knowledge of the owner.
One should never lose sight that the facility/asset owner, contractor, and coating inspector share a common goal: Provide long term corrosion protection of the structure or asset. Working together to execute the specification should be the mantra. The relationship between the contractor and inspector needn’t be adversarial if each understands the common goal and the pathway to achieve that goal.
Summary
The value that a well-trained, competent coating inspector brings to a project cannot be overstated. Inspectors can help prevent or reduce rework that adversely impacts schedule and/or results in cost overruns and can help prevent premature coating failure. Initial training, coaching/ mentoring, continuing education, experience, and both verbal and written communication skills are all key to a competent coating inspector. Complete, thorough knowledge of industry standards and instrument use combined with high personal integrity and a strong work ethic to enforce the specification without personal bias are equally important. When all these KSAs of a competent coating inspector are brought to bear on a coatings project they can help to achieve the common goal: long term corrosion protection of the asset or facility.
Instrument | Purpose | Reference Standard(s) |
Air & Dew Point Temperature Meter; Relative Humidity Meter | Measure prevailing ambient conditions prior to final surface preparation, prior to coating mixing, and during coating application | ASTM E337 |
Surface Temperature Thermometer | Verify the surface temperature is a minimum of 5°F higher than the dew point temperature (and rising) | SSPC- PA 1 |
Rotating Vane Anemometer | Determine conformance to minimum air flow (ventilation) requirements inside containment | SSPC Guide 6 |
Light Meter | Determine conformance to minimum illumination requirements for the work area as well as surface preparation/coating application and inspection operations | SSPC Guide 12 |
Abrasive Contamination Test Kit | Determine conformance to maximum water-soluble contaminant levels on new and reused abrasive | SSPC Abrasive Standards AB 1, AB 2, AB 3, AB 4 |
Blast Nozzle Orifice Gage | Monitor blast nozzle wear | NA |
Hypodermic Needle Pressure Gage | Monitor minimum blast nozzle pressure | NA |
Blotter Paper | Verify compressed air does not contain visible oil or water | ASTM D4285 |
Spring Micrometer or Replica Tape Reader with Replica Tape | Measure the resulting surface profile depth after abrasive blast cleaning | ASTM D4417, Method C |
Depth Micrometer | Measure the resulting surface profile depth after power tool and/or abrasive blast cleaning | ASTM D4417, Method B; SSPC-SP 15; SSPC-SP 11 |
Surface Contamination Analysis Test (SCAT) Kit | Verify surface salt contamination levels do not exceed acceptable levels, per specification | Per Project Specification |
SSPC Visual (VIS) Guides | Aid in assessing surface cleanliness | SSPC Surface Preparation Standards |
Dull Putty Knife | Aid in determining loosely versus tightly adhering materials | SSPC Surface Preparation Standards |
Wet Film Thickness Gage | Determine the speed and number of spray passes to achieve to correct film build | ASTM D4414 |
Dry Film Thickness Gage | Determine the thickness of individual coating layers | SSPC-PA 2 |
Certified Coated Standards | Verify the accuracy of a dry film thickness gage | ASTM D7091; SSPC-PA 2 |
Wall Thickness Gage | Determine section loss of a material like steel | NA |
Inspection Mirror | Aid with visual inspection of difficult access areas | NA |
Low Voltage Pinhole Detector | Detect pinholes/discontinuities in a lining system | ASTM D5162 |
Tape/Knife Adhesion Test Kit | Assess the adhesive/cohesive properties and a coating system | ASTM D3359; D6677 |
Hardness Tester | Determine the cure of a coating prior to service | ASTM D2240 |
[1] The Inspection of Coatings and Linings, SSPC: The Society for Protective Coatings Publication 97-07, Chapter 2, Inspection Personnel, Kenneth B. Tator
[2] W.D. Corbett (2016). Industry Standards: Are You Current? Proceedings of the SSPC National Conference and Exhibition, 2016.
[3] AMPP-SSPC Qualification Procedure No. 5, Standard Procedure for Evaluating the Qualifications of Coating and Lining Inspection Companies, AMPP: Association for Materials Protection & Performance.
[4] ASTM D3276 Standard Guide for Painting Inspectors (Metal Substrates), Volume 06.01, ASTM International, Conshohocken, PA USA
[5] ASTM D6237, Standard Guide for Painting Inspectors (Concrete and Masonry Substrates), Volume 06.01, ASTM International, Conshohocken, PA USA
[6] Using Coatings Inspection Instruments, 3rd Edition (2012), W.D. Corbett, KTA-Tator, Inc., Pittsburgh, PA USA